
Plant Foreman
Resume Work Experience Examples & Samples
Overview of Plant Foreman
A Plant Foreman is a supervisory role in a manufacturing or industrial setting. They are responsible for overseeing the daily operations of the plant, ensuring that production goals are met, and that all safety protocols are followed. The Plant Foreman also manages a team of workers, assigns tasks, and provides guidance and support as needed. This role requires strong leadership skills, as well as a deep understanding of the production process and the machinery involved.
The Plant Foreman must also be able to troubleshoot and solve problems quickly, as issues can arise at any time during production. They must be able to communicate effectively with both their team and upper management, and be able to adapt to changing circumstances. This role is critical to the success of the plant, as the Plant Foreman is responsible for ensuring that production runs smoothly and efficiently.
About Plant Foreman Resume
A Plant Foreman resume should highlight the candidate's experience in managing and supervising a team of workers, as well as their knowledge of the production process. The resume should also emphasize the candidate's ability to meet production goals, maintain safety protocols, and troubleshoot and solve problems quickly. It is important to include any relevant certifications or training that the candidate has received, as well as any awards or recognition they have received for their work.
The resume should also highlight the candidate's leadership skills, as well as their ability to communicate effectively with both their team and upper management. It is important to include any experience the candidate has with adapting to changing circumstances, as this is a key aspect of the Plant Foreman role. The resume should be well-organized and easy to read, with clear headings and bullet points to make it easy for potential employers to quickly identify the candidate's qualifications.
Introduction to Plant Foreman Resume Work Experience
The work-experience section of a Plant Foreman resume should include a detailed description of the candidate's previous roles, with a focus on their responsibilities as a supervisor or manager. It is important to include specific examples of how the candidate has contributed to the success of the plant, such as by meeting production goals, improving safety protocols, or increasing efficiency. The work-experience section should also highlight the candidate's ability to manage a team of workers, assign tasks, and provide guidance and support as needed.
The work-experience section should also include any experience the candidate has with troubleshooting and solving problems quickly, as well as their ability to communicate effectively with both their team and upper management. It is important to include any experience the candidate has with adapting to changing circumstances, as this is a key aspect of the Plant Foreman role. The work-experience section should be well-organized and easy to read, with clear headings and bullet points to make it easy for potential employers to quickly identify the candidate's qualifications.
Examples & Samples of Plant Foreman Resume Work Experience
Plant Foreman at ABC Manufacturing
Led a team of 20 workers in the production of high-quality steel products. Implemented new safety protocols that reduced workplace accidents by 30%. Successfully managed production schedules to meet tight deadlines and increased output by 15%. (2018 - 2021)
Plant Foreman at XYZ Industries
Oversaw daily operations of a 100-employee manufacturing plant. Introduced lean manufacturing techniques that improved efficiency by 20%. Managed inventory and supply chain to ensure timely delivery of products. (2015 - 2018)
Plant Foreman at DEF Corporation
Supervised the assembly line production of automotive parts. Trained new employees on safety and production standards. Reduced production costs by 10% through process optimization. (2012 - 2015)

View Examples for Other Jobs:
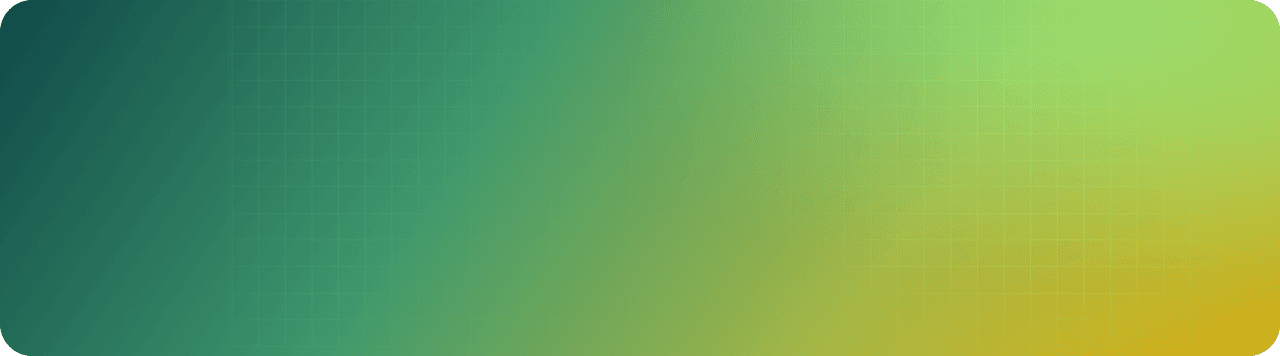