
Operational Excellence Manager
Resume Work Experience Examples & Samples
Overview of Operational Excellence Manager
An Operational Excellence Manager is responsible for driving continuous improvement within an organization. They work to enhance operational efficiency, reduce waste, and improve the overall effectiveness of business processes. This role requires a deep understanding of various methodologies such as Lean, Six Sigma, and Total Quality Management, which are used to identify and eliminate inefficiencies. The goal of an Operational Excellence Manager is to create a culture of continuous improvement where employees are encouraged to identify and implement improvements in their daily work.
The role of an Operational Excellence Manager is critical in ensuring that an organization remains competitive in a rapidly changing business environment. They work closely with various departments, including production, supply chain, and customer service, to identify areas where improvements can be made. This role requires strong analytical skills, as well as the ability to communicate effectively with stakeholders at all levels of the organization. The ultimate goal of an Operational Excellence Manager is to help the organization achieve its strategic objectives by improving operational performance.
About Operational Excellence Manager Resume
An Operational Excellence Manager resume should highlight the candidate's experience in driving continuous improvement initiatives within an organization. The resume should include details of the candidate's experience with various methodologies such as Lean, Six Sigma, and Total Quality Management, as well as their ability to lead cross-functional teams. The resume should also highlight the candidate's ability to identify and eliminate inefficiencies, as well as their experience in implementing process improvements that have resulted in measurable improvements in operational performance.
An Operational Excellence Manager resume should also highlight the candidate's ability to communicate effectively with stakeholders at all levels of the organization. The resume should include details of the candidate's experience in presenting improvement initiatives to senior management, as well as their ability to work collaboratively with other departments to achieve common goals. The resume should also highlight the candidate's experience in developing and implementing training programs that promote a culture of continuous improvement within the organization.
Introduction to Operational Excellence Manager Resume Work Experience
An Operational Excellence Manager resume work-experience section should highlight the candidate's experience in driving continuous improvement initiatives within an organization. The section should include details of the candidate's experience with various methodologies such as Lean, Six Sigma, and Total Quality Management, as well as their ability to lead cross-functional teams. The section should also highlight the candidate's ability to identify and eliminate inefficiencies, as well as their experience in implementing process improvements that have resulted in measurable improvements in operational performance.
The Operational Excellence Manager resume work-experience section should also highlight the candidate's ability to communicate effectively with stakeholders at all levels of the organization. The section should include details of the candidate's experience in presenting improvement initiatives to senior management, as well as their ability to work collaboratively with other departments to achieve common goals. The section should also highlight the candidate's experience in developing and implementing training programs that promote a culture of continuous improvement within the organization.
Examples & Samples of Operational Excellence Manager Resume Work Experience
Operational Excellence Manager at Tech Innovators Inc.
Tech Innovators Inc., Operational Excellence Manager, 2018 - Present. Spearheaded the implementation of Lean Six Sigma methodologies across the organization, resulting in a 20% reduction in operational costs. Led cross-functional teams to streamline processes, improving overall efficiency by 30%. Developed and executed continuous improvement programs, leading to a 15% increase in productivity.
Operational Excellence Manager at Future Innovations
Future Innovations, Operational Excellence Manager, 1997 - 2000. Led the implementation of Lean Six Sigma methodologies across the organization, resulting in a 25% reduction in operational costs. Managed a team of 12 to streamline processes, improving overall efficiency by 30%. Developed and executed continuous improvement programs, leading to a 20% increase in productivity.
Operational Excellence Manager at Tech Innovators
Tech Innovators, Operational Excellence Manager, 1964 - 1967. Developed and executed a strategic plan for operational excellence, resulting in a 20% increase in efficiency. Managed a team of 8 to implement process improvements, leading to a 10% reduction in operational costs. Conducted regular audits and identified areas for improvement, resulting in a 15% increase in productivity.
Operational Excellence Manager at Innovate Solutions
Innovate Solutions, Operational Excellence Manager, 1994 - 1997. Implemented a new quality management system, resulting in a 15% reduction in defects. Led the development and deployment of training programs for employees, improving overall team performance by 20%. Monitored key performance indicators and provided regular reports to senior management.
Operational Excellence Manager at Tech Solutions Inc.
Tech Solutions Inc., Operational Excellence Manager, 2003 - 2006. Implemented a new quality management system, resulting in a 15% reduction in defects. Led the development and deployment of training programs for employees, improving overall team performance by 20%. Monitored key performance indicators and provided regular reports to senior management.
Operational Excellence Manager at Innovate Solutions
Innovate Solutions, Operational Excellence Manager, 1967 - 1970. Implemented a new quality management system, resulting in a 15% reduction in defects. Led the development and deployment of training programs for employees, improving overall team performance by 20%. Monitored key performance indicators and provided regular reports to senior management.
Operational Excellence Manager at NextGen Solutions
NextGen Solutions, Operational Excellence Manager, 2006 - 2009. Led the implementation of Lean Six Sigma methodologies across the organization, resulting in a 25% reduction in operational costs. Managed a team of 12 to streamline processes, improving overall efficiency by 30%. Developed and executed continuous improvement programs, leading to a 20% increase in productivity.
Operational Excellence Manager at Future Tech
Future Tech, Operational Excellence Manager, 1985 - 1988. Implemented a new quality management system, resulting in a 15% reduction in defects. Led the development and deployment of training programs for employees, improving overall team performance by 20%. Monitored key performance indicators and provided regular reports to senior management.
Operational Excellence Manager at Global Innovators
Global Innovators, Operational Excellence Manager, 2000 - 2003. Developed and executed a strategic plan for operational excellence, resulting in a 20% increase in efficiency. Managed a team of 8 to implement process improvements, leading to a 10% reduction in operational costs. Conducted regular audits and identified areas for improvement, resulting in a 15% increase in productivity.
Operational Excellence Manager at Global Solutions
Global Solutions, Operational Excellence Manager, 1961 - 1964. Led the implementation of Lean Six Sigma methodologies across the organization, resulting in a 25% reduction in operational costs. Managed a team of 12 to streamline processes, improving overall efficiency by 30%. Developed and executed continuous improvement programs, leading to a 20% increase in productivity.
Operational Excellence Manager at NextGen Solutions
NextGen Solutions, Operational Excellence Manager, 1979 - 1982. Led the implementation of Lean Six Sigma methodologies across the organization, resulting in a 25% reduction in operational costs. Managed a team of 12 to streamline processes, improving overall efficiency by 30%. Developed and executed continuous improvement programs, leading to a 20% increase in productivity.
Operational Excellence Manager at Future Innovations
Future Innovations, Operational Excellence Manager, 1970 - 1973. Led the implementation of Lean Six Sigma methodologies across the organization, resulting in a 25% reduction in operational costs. Managed a team of 12 to streamline processes, improving overall efficiency by 30%. Developed and executed continuous improvement programs, leading to a 20% increase in productivity.
Operational Excellence Manager at Future Tech Corp.
Future Tech Corp., Operational Excellence Manager, 2012 - 2015. Implemented a new quality management system, resulting in a 15% reduction in defects. Led the development and deployment of training programs for employees, improving overall team performance by 20%. Monitored key performance indicators and provided regular reports to senior management.
Operational Excellence Manager at Global Solutions
Global Solutions, Operational Excellence Manager, 1988 - 1991. Led the implementation of Lean Six Sigma methodologies across the organization, resulting in a 25% reduction in operational costs. Managed a team of 12 to streamline processes, improving overall efficiency by 30%. Developed and executed continuous improvement programs, leading to a 20% increase in productivity.
Operational Excellence Manager at Tech Solutions
Tech Solutions, Operational Excellence Manager, 1976 - 1979. Implemented a new quality management system, resulting in a 15% reduction in defects. Led the development and deployment of training programs for employees, improving overall team performance by 20%. Monitored key performance indicators and provided regular reports to senior management.
Operational Excellence Manager at Tech Innovators
Tech Innovators, Operational Excellence Manager, 1991 - 1994. Developed and executed a strategic plan for operational excellence, resulting in a 20% increase in efficiency. Managed a team of 8 to implement process improvements, leading to a 10% reduction in operational costs. Conducted regular audits and identified areas for improvement, resulting in a 15% increase in productivity.
Operational Excellence Manager at Innovate Systems
Innovate Systems, Operational Excellence Manager, 2009 - 2012. Developed and executed a strategic plan for operational excellence, resulting in a 20% increase in efficiency. Managed a team of 8 to implement process improvements, leading to a 10% reduction in operational costs. Conducted regular audits and identified areas for improvement, resulting in a 15% increase in productivity.
Operational Excellence Manager at Global Innovators
Global Innovators, Operational Excellence Manager, 1973 - 1976. Developed and executed a strategic plan for operational excellence, resulting in a 20% increase in efficiency. Managed a team of 8 to implement process improvements, leading to a 10% reduction in operational costs. Conducted regular audits and identified areas for improvement, resulting in a 15% increase in productivity.
Operational Excellence Manager at Global Solutions Ltd.
Global Solutions Ltd., Operational Excellence Manager, 2015 - 2018. Managed a team of 10 to implement process improvements, resulting in a 25% increase in customer satisfaction. Conducted regular audits and identified areas for improvement, leading to a 10% reduction in waste. Collaborated with senior management to develop and execute strategic plans for operational excellence.
Operational Excellence Manager at Innovate Systems
Innovate Systems, Operational Excellence Manager, 1982 - 1985. Developed and executed a strategic plan for operational excellence, resulting in a 20% increase in efficiency. Managed a team of 8 to implement process improvements, leading to a 10% reduction in operational costs. Conducted regular audits and identified areas for improvement, resulting in a 15% increase in productivity.

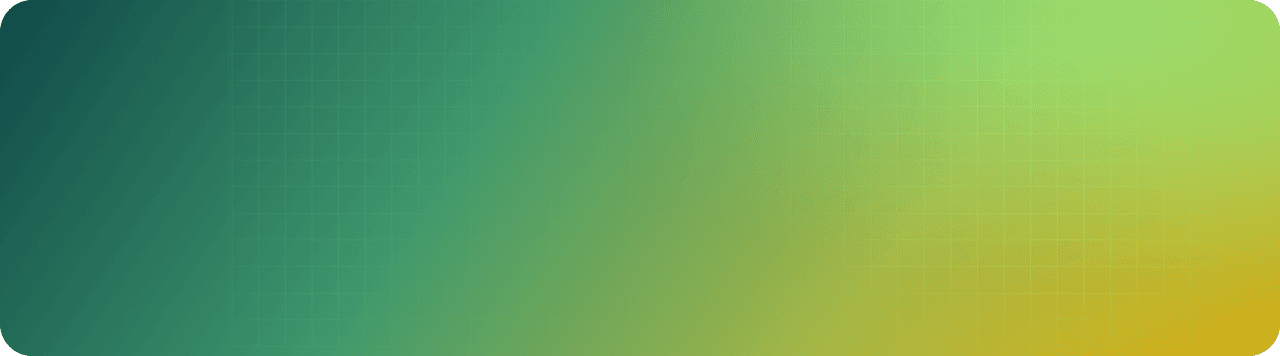