
Field Quality Assurance
Resume Work Experience Examples & Samples
Overview of Field Quality Assurance
Field Quality Assurance is a critical function in various industries, ensuring that products and services meet the required standards and specifications. This field involves the systematic monitoring and evaluation of various aspects of a product or service, from the initial concept to the final delivery. Quality assurance professionals are responsible for identifying potential issues, implementing corrective actions, and ensuring compliance with industry regulations and standards.
The role of a Field Quality Assurance professional is multifaceted, requiring a combination of technical skills, attention to detail, and strong problem-solving abilities. They work closely with other departments, such as production, engineering, and customer service, to ensure that quality is maintained throughout the entire process. Effective communication and collaboration are essential, as quality assurance professionals must be able to convey complex information to a variety of stakeholders.
About Field Quality Assurance Resume
A Field Quality Assurance resume should highlight the candidate's experience and expertise in ensuring product quality and compliance with industry standards. It should include relevant work experience, education, certifications, and any specialized training in quality assurance methodologies and tools. The resume should also emphasize the candidate's ability to identify and resolve quality issues, as well as their experience in implementing quality control processes.
When crafting a Field Quality Assurance resume, it is important to focus on the candidate's achievements and contributions to previous roles. This includes any successful quality improvement initiatives, cost savings, or process optimizations. The resume should also highlight any leadership or management experience, as well as any experience working in regulated industries or with high-risk products.
Introduction to Field Quality Assurance Resume Work Experience
The work-experience section of a Field Quality Assurance resume should provide a detailed account of the candidate's professional history, including their roles, responsibilities, and achievements. This section should be organized chronologically, starting with the most recent position and working backwards. Each job entry should include a brief description of the company and the candidate's role, as well as a list of key responsibilities and accomplishments.
When writing the work-experience section, it is important to use specific and quantifiable examples to demonstrate the candidate's impact on quality assurance. This includes any successful quality audits, process improvements, or corrective actions implemented. The section should also highlight any experience with quality management systems, such as ISO 9001, and any experience working with regulatory bodies or third-party auditors.
Examples & Samples of Field Quality Assurance Resume Work Experience
Quality Assurance Analyst
VWX Enterprises, Quality Assurance Analyst, 1998-2000. Conducted field inspections and audits to ensure product quality. Identified and resolved quality issues, resulting in a 15% reduction in product defects. Trained new inspectors on quality control procedures.
Quality Assurance Specialist
ABC Corporation, Quality Assurance Specialist, 2018-2021. Responsible for conducting field inspections and ensuring compliance with company standards. Implemented a new inspection protocol that reduced inspection time by 20%. Achieved a 98% customer satisfaction rate.
Quality Assurance Manager
EFG Enterprises, Quality Assurance Manager, 2010-2012. Managed the quality assurance department and supervised field inspections. Implemented a new quality management system that improved compliance by 30%. Achieved a 99% customer satisfaction rate.
Quality Control Inspector
DEF Manufacturing, Quality Control Inspector, 1992-1994. Conducted routine inspections and audits to ensure product quality. Identified and resolved quality issues, resulting in a 10% reduction in product defects. Trained new inspectors on quality control procedures.
Field Quality Assurance Technician
LMN Technologies, Field Quality Assurance Technician, 2014-2016. Performed on-site inspections and testing to ensure product compliance. Collaborated with production teams to improve quality processes. Achieved a 95% compliance rate with industry standards.
Quality Assurance Specialist
JKL Corporation, Quality Assurance Specialist, 1988-1990. Responsible for conducting field inspections and ensuring compliance with company standards. Implemented a new inspection protocol that reduced inspection time by 20%. Achieved a 98% customer satisfaction rate.
Quality Control Manager
YZA Corporation, Quality Control Manager, 1996-1998. Managed the quality control department and supervised field inspections. Implemented a new quality management system that improved compliance by 25%. Achieved a 98% customer satisfaction rate.
Field Quality Assurance Technician
GHI Technologies, Field Quality Assurance Technician, 1990-1992. Performed on-site inspections and testing to ensure product compliance. Collaborated with production teams to improve quality processes. Achieved a 95% compliance rate with industry standards.
Quality Control Supervisor
MNO Industries, Quality Control Supervisor, 1986-1988. Supervised a team of quality control inspectors and conducted field inspections. Implemented a new inspection protocol that reduced inspection time by 15%. Achieved a 97% compliance rate with industry standards.
Quality Assurance Inspector
STU Manufacturing, Quality Assurance Inspector, 1982-1984. Conducted routine inspections and audits to ensure product quality. Identified and resolved quality issues, resulting in a 10% reduction in product defects. Trained new inspectors on quality control procedures.
Field Quality Assurance Specialist
VWX Solutions, Field Quality Assurance Specialist, 1980-1982. Performed on-site inspections and testing to ensure product compliance. Collaborated with production teams to improve quality processes. Achieved a 95% compliance rate with industry standards.
Quality Control Inspector
XYZ Industries, Quality Control Inspector, 2016-2018. Conducted routine inspections and audits to ensure product quality. Identified and resolved quality issues, resulting in a 15% reduction in product defects. Trained new inspectors on quality control procedures.
Field Quality Assurance Specialist
STU Solutions, Field Quality Assurance Specialist, 2000-2002. Performed on-site inspections and testing to ensure product compliance. Collaborated with production teams to improve quality processes. Achieved a 95% compliance rate with industry standards.
Quality Assurance Supervisor
BCD Industries, Quality Assurance Supervisor, 1994-1996. Supervised a team of quality assurance professionals in conducting field inspections. Developed and implemented quality assurance policies and procedures. Reduced inspection errors by 20%.
Quality Assurance Engineer
HIJ Manufacturing, Quality Assurance Engineer, 2008-2010. Designed and implemented quality assurance processes and procedures. Conducted field inspections and audits to ensure product quality. Reduced product defects by 20%.
Quality Assurance Coordinator
NOP Industries, Quality Assurance Coordinator, 2004-2006. Coordinated field inspections and audits to ensure product quality. Collaborated with production teams to improve quality processes. Achieved a 95% compliance rate with industry standards.
Quality Assurance Inspector
QRS Manufacturing, Quality Assurance Inspector, 2002-2004. Conducted routine inspections and audits to ensure product quality. Identified and resolved quality issues, resulting in a 10% reduction in product defects. Trained new inspectors on quality control procedures.
Senior Quality Assurance Analyst
PQR Solutions, Senior Quality Assurance Analyst, 2012-2014. Led a team of quality assurance professionals in conducting field inspections. Developed and implemented quality assurance policies and procedures. Reduced inspection errors by 25%.
Quality Assurance Coordinator
PQR Solutions, Quality Assurance Coordinator, 1984-1986. Coordinated field inspections and audits to ensure product quality. Collaborated with production teams to improve quality processes. Achieved a 95% compliance rate with industry standards.
Quality Control Supervisor
KLM Corporation, Quality Control Supervisor, 2006-2008. Supervised a team of quality control inspectors and conducted field inspections. Implemented a new inspection protocol that reduced inspection time by 15%. Achieved a 97% compliance rate with industry standards.

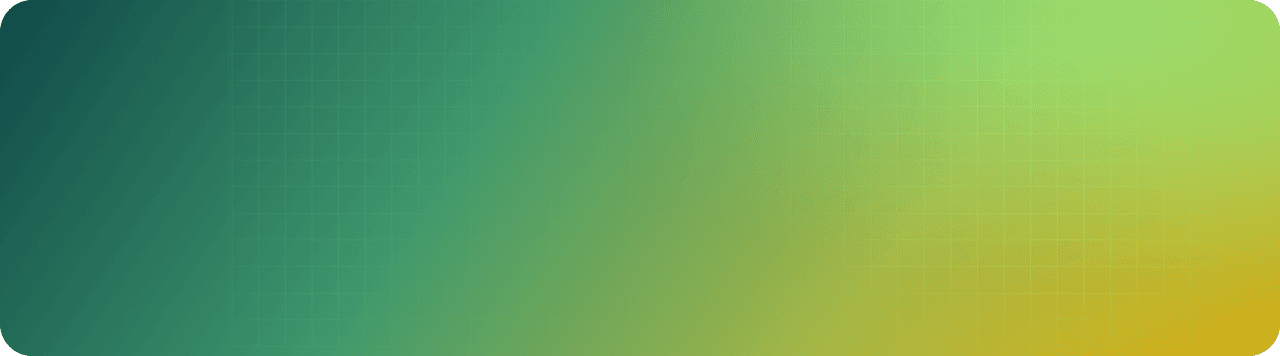