
Equipment Coordinator
Resume Work Experience Examples & Samples
Overview of Equipment Coordinator
An Equipment Coordinator is responsible for the management and maintenance of equipment used in various industries such as construction, manufacturing, and healthcare. They ensure that all equipment is in good working condition, schedule maintenance and repairs, and manage inventory levels to prevent shortages or overstock. The role requires strong organizational skills, attention to detail, and the ability to work well under pressure.
An Equipment Coordinator also plays a crucial role in ensuring safety in the workplace by ensuring that all equipment is properly maintained and used according to safety guidelines. They may also be responsible for training employees on the proper use of equipment and ensuring that all safety protocols are followed. The job requires a good understanding of the equipment used in the industry, as well as the ability to troubleshoot and solve problems quickly.
About Equipment Coordinator Resume
An Equipment Coordinator resume should highlight the candidate's experience in managing and maintaining equipment, as well as their ability to work well under pressure and ensure safety in the workplace. The resume should include details of the candidate's previous roles, the types of equipment they have managed, and any relevant certifications or training they have received.
The resume should also highlight the candidate's organizational skills, attention to detail, and ability to work well with others. It should include any experience the candidate has in scheduling maintenance and repairs, managing inventory levels, and training employees on the proper use of equipment.
Introduction to Equipment Coordinator Resume Work Experience
The work-experience section of an Equipment Coordinator resume should provide a detailed account of the candidate's previous roles, including the types of equipment they have managed, the size of the teams they have worked with, and the scope of their responsibilities. It should also include any achievements or successes the candidate has had in their previous roles, such as reducing downtime or improving safety records.
The work-experience section should also highlight the candidate's ability to troubleshoot and solve problems quickly, as well as their experience in scheduling maintenance and repairs, managing inventory levels, and training employees on the proper use of equipment. It should provide a clear picture of the candidate's experience and qualifications, and demonstrate their ability to excel in the role of Equipment Coordinator.
Examples & Samples of Equipment Coordinator Resume Work Experience
Equipment Coordinator at ZAB Manufacturing
Assisted in the maintenance and repair of all manufacturing equipment. Monitored equipment performance and reported any issues to the supervisor. 1982 - 1984
Equipment Coordinator at ABC Manufacturing
Responsible for coordinating the maintenance and repair of all manufacturing equipment. Successfully reduced downtime by 15% through proactive maintenance scheduling. Worked closely with vendors to ensure timely delivery of parts and supplies. 2018 - 2020
Equipment Coordinator at TUV Industries
Managed a team of 20 technicians to ensure all equipment was operational and met safety standards. Implemented a new inventory system that reduced equipment costs by 25%. 1986 - 1988
Equipment Coordinator at HIJ Corporation
Coordinated the installation and calibration of new equipment. Trained new employees on equipment operation and safety protocols. 1994 - 1996
Equipment Coordinator at WXY Corporation
Coordinated the installation and calibration of new equipment. Trained new employees on equipment operation and safety protocols. 1984 - 1986
Equipment Coordinator at YZA Manufacturing
Managed the inventory of all equipment and supplies. Coordinated with vendors to ensure timely delivery of parts and supplies. 2000 - 2002
Equipment Coordinator at KLM Industries
Assisted in the maintenance and repair of all manufacturing equipment. Monitored equipment performance and reported any issues to the supervisor. 1992 - 1994
Equipment Coordinator at GHI Manufacturing
Assisted in the maintenance and repair of all manufacturing equipment. Monitored equipment performance and reported any issues to the supervisor. 2012 - 2014
Equipment Coordinator at EFG Manufacturing
Managed a team of 15 technicians to ensure all equipment was operational and met safety standards. Implemented a new inventory system that reduced equipment costs by 20%. 1996 - 1998
Equipment Coordinator at XYZ Industries
Managed a team of 5 technicians to ensure all equipment was operational and met safety standards. Implemented a new inventory system that reduced equipment costs by 10%. 2016 - 2018
Equipment Coordinator at MNO Corporation
Responsible for the maintenance and repair of all manufacturing equipment. Implemented a new maintenance schedule that reduced downtime by 20%. 2008 - 2010
Equipment Coordinator at QRS Corporation
Responsible for the maintenance and repair of all manufacturing equipment. Implemented a new maintenance schedule that reduced downtime by 30%. 1988 - 1990
Equipment Coordinator at VWX Corporation
Assisted in the maintenance and repair of all manufacturing equipment. Monitored equipment performance and reported any issues to the supervisor. 2002 - 2004
Equipment Coordinator at DEF Corporation
Coordinated the installation and calibration of new equipment. Trained new employees on equipment operation and safety protocols. 2014 - 2016
Equipment Coordinator at PQR Manufacturing
Managed a team of 10 technicians to ensure all equipment was operational and met safety standards. Implemented a new inventory system that reduced equipment costs by 15%. 2006 - 2008
Equipment Coordinator at CDE Industries
Managed the inventory of all equipment and supplies. Coordinated with vendors to ensure timely delivery of parts and supplies. 1980 - 1982
Equipment Coordinator at NOP Manufacturing
Managed the inventory of all equipment and supplies. Coordinated with vendors to ensure timely delivery of parts and supplies. 1990 - 1992
Equipment Coordinator at STU Industries
Coordinated the installation and calibration of new equipment. Trained new employees on equipment operation and safety protocols. 2004 - 2006
Equipment Coordinator at BCD Industries
Responsible for the maintenance and repair of all manufacturing equipment. Implemented a new maintenance schedule that reduced downtime by 25%. 1998 - 2000
Equipment Coordinator at JKL Industries
Managed the inventory of all equipment and supplies. Coordinated with vendors to ensure timely delivery of parts and supplies. 2010 - 2012

View Examples for Other Jobs:
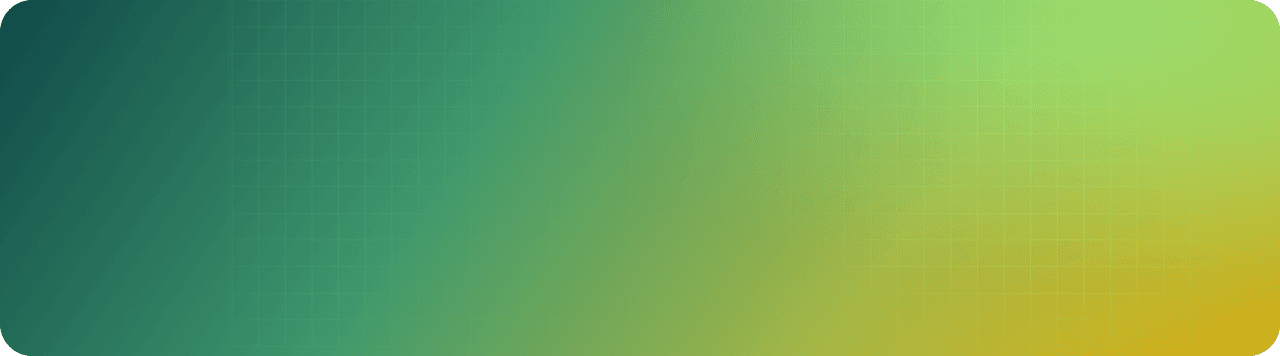